A Shortage of Skilled Workers Threatens Manufacturing’s Rebound
U.S. manufacturers will create more than 3 million job openings over the next decade – but two million of these future jobs could go unfilled.
Politicians and policymakers of all political stripes have long made growing U.S. manufacturing jobs a top priority. President Donald Trump, for example, has been an especially vocal advocate of rebuilding U.S. manufacturing as an antidote to the offshoring of jobs.
The good news is that the U.S. manufacturing renaissance is in fact already underway. According to government labor statistics, the sector has added more than 895,000 jobs since the end of 2010 and expects to create at least another 700,000 jobs by the end of the decade, according to industry analysts. Add in the pending retirement of the Baby Boomers, and U.S. manufacturers say they’ll need to fill as many as 3.5 million jobs over the next ten years.
A looming shortage of skilled workers, however, could cut this nascent renaissance short. In its Skills Gap report updated every four years or so, the industry’s Manufacturing Institute predicts that as many as 2 million future jobs could go unfilled from the lack of workers with the right technology, computer and technical skills.
While employers in a variety of sectors have complained of a “skills gap” in the current workforce – leading some to question its true extent – the manufacturing skills gap is unique. For one thing, continuing negative public perceptions of manufacturing job – as dirty, dangerous, and with low job security – are a major reason why the talent pool remains small.“The general public is very supportive of manufacturing – in the abstract,” says Gardner Carrick, Vice President of Strategic Initiatives at the Manufacturing Institute. “[People] understand the multiplier effect that comes with manufacturing and want the jobs in their backyard – just not for them or their families.”
The Manufacturing Institute’s study, for example, reports that just 37 percent of parents would encourage their children to pursue careers in manufacturing, and 52 percent of teens say they have no interest in manufacturing jobs. Meanwhile, the average wage of manufacturing workers in 2013 was $77,506, and most manufacturing jobs now require some sort of post-secondary credential.
Changing public perceptions to match the modern realities of U.S. manufacturing will be critical to addressing the worker shortage, Carrick says, especially among millennials. Also important: rebuilding a pipeline of potential recruits through high school and career technical programs.
This interview has been edited for length and clarity.
How are today’s manufacturing jobs different from the past?
Carrick: Manufacturing jobs have certainly changed compared to what they were a generation or two ago and what the perception of them may still be.Nearly all of the jobs that were unskilled or semi-skilled have either been automated out of existence or moved offshore in search of cheaper labor. The jobs that are remaining in manufacturing are really focused on operating, maintaining or programming the machines that are doing a lot of the actual manual labor and hard work that used to be done by human beings.
What kind of skills does that mean workers need?
Carrick: [Workers today] need a higher degree of technical skills; they need a better understanding of the technology that’s running these machines; and they need to be able to interact with these machines on the fly, which requires a degree of problem-solving skill. When we asked manufacturers what they’re not seeing in their current workforce, two-thirds or more of manufacturers told us that technology skills are lacking, that basic technical skills are lacking, and that problem-solving skills are lacking. Those skills are the ones that are in the most demand for manufacturers and are the hardest to find these days.
Why are these skills so tough to find in younger workers?
Carrick: On the technical skills side, you really saw a hollowing out of the manufacturing education system over the last 25 to 30 years. And that’s true both on the company side and the education system side. You saw the reduction or the outright elimination of many of the [vocational and technical] programs available to high schools around the country. You saw companies scaling back or eliminating apprenticeship programs that were prevalent in the 1940s, ‘50s and ‘60s.
It was a logical approach on both sides because of the real reduction in jobs available in manufacturing and the belief that manufacturing was disappearing. It was a prudent and logical decision at the time it was made, but now that manufacturing has rebounded, those programs to train individuals to enter those careers simply aren’t there anymore. We need to restart them through a combination of programs run or offered by manufacturers and by high schools or at the college level.
What’s your best argument to millennials that they should consider careers in manufacturing?
Carrick: If you’re looking for a career that has upward mobility, offers competitive starting wages and really excellent wages across your entire career span, then manufacturing is for you. Oftentimes you see the press focusing on entry-level wages in manufacturing and saying those aren’t competitive, but manufacturing offers an array of career paths – many of which lead to six-figure salaries.
And if you’re looking to solve some of the biggest challenges the world faces – whether from a technology standpoint or from an environmental standpoint or really from any standpoint – those challenges must be addressed and solved through manufacturing. Manufacturing is the one industry that wraps those things together. It’s a very attractive career option for a millennial who wants to make a difference but still wants to make money and have a rewarding career.
How are you trying to change public perceptions of manufacturing?
Carrick: It’s not going to happen overnight, but I think we’re beginning to see some changes in perception. One of the most interesting things we found this year is that individuals who self-identify as being familiar with manufacturing were twice as likely to encourage their child to pursue a career in the industry. I think that begins to validate the work that we at the Manufacturing Institute have done in trying to expose more people to careers in manufacturing.
Our biggest initiative is Manufacturing Day on the first Friday in October. In 2016, we had almost 600,000 individuals participate in plant tours of manufacturing facilities in their community, nearly 268,000 of them students. What that does is really demystify manufacturing. It shows that manufacturers have a very advanced workplace – a very clean and safe workplace, and offers a very desirable career. When you couple that with stories about the renaissance of manufacturing, you can combat what was 25 or 30 years of negative press around manufacturing.
Why is manufacturing rebounding?
Carrick: Beginning in the early 2000s, you saw lots of companies rushing overseas, in particular to China and other East Asian countries in search of cheap labor. What was less apparent at the time were some of the hidden costs of operating in East Asia. These include relatively easy costs to calculate, such as transportation costs. There was also the cost of time lost. It takes several weeks to ship things across the Pacific, and when consumers are demanding goods both more quickly and in a more customized way, that creates a problem.
Another cost of operating overseas was [the risk to] intellectual property. Manufacturers that were particularly dependent on intellectual property were taking a risk by working in places that did not have the same level of respect for intellectual property as the United States does.
All of those cost aspects began to coalesce into a situation where it was no longer obvious that you needed to be in Asia. And when you combine that with the tremendous energy resources that we’ve in the United States – we’re really able to make the case that doing business in the United States and producing goods in the United States is in fact cheaper today than it would be in East Asia.
What specific policies do you recommend for fixing the skills gap?
Carrick: Interestingly, this is not a federal policy arena. This is not to say that there aren’t important federal policies. The Workforce Innovation and Opportunity Act, enacted in July 2015, updated the job training system in the United States to make it more reflective of today’s world. There’s certainly the Carl D. Perkins [Career and Technical Education] Act, which funds technical education in high school.
But when you’re talking about education, you’re really talking about state policies and local decisions that impact what programs to invest in, what companies to engage with and how those programs are designed.
We’ve tried to highlight a few efforts that we think really begin to change the quality of manufacturing education offered in the states. It can be as simple as offering incentives to schools that have their students achieve industry-recognized credentials – Kansas is the probably the best example of that.
In Tennessee, the “Drive to 55” is a good example that looks to expand the focus beyond your traditional baccalaureate and associate degree programs into those industry credential offerings that do make a difference in the labor market.
We’re pleased to see that states are really picking up on how to expand or improve the number of citizens in their state who have earned the credentials they need to be successful in the workplace.
What’s the cost to companies and to the economy if the manufacturing worker shortage isn’t fixed?
Carrick: We found that there’s potentially a loss of up to 11 percent of net earnings for individual companies if they’re unable to fill open positions. So yes, it hurts the bottom line of companies – but it also hurts the United States as a whole.
Manufacturing is probably the most important industry to the U.S. economy – not just in terms of overall GDP but because it’s really the engine that drives much of the private sector economy. You see that in the multiplier effect, and you see that in R&D.
For the entire 20th century, the United States enjoyed a tremendous advantage in manufacturing. We now have an opportunity to reestablish that advantage through this renaissance in “reshoring” that’s happened over the last four or five years. If we’re not able to ensure a skilled workforce and a steady supply of skilled workers for manufacturers in this country, then they’re either going to go out of business or be forced to look elsewhere.
Gardner Carrick is Vice President of Strategic Initiatives at the Manufacturing Institute.
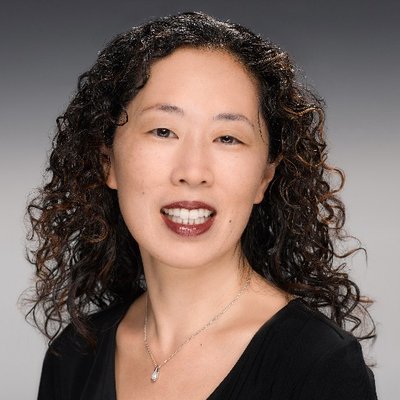
Anne is Vice President of Domestic Policy at the Progressive Policy Institute and a contributing editor at the Washington Monthly.